Hazardous gases, hazardous liquids, flammable and explosive products in the chemical industry, special nitrogen generator for purging: generally use nitrogen purity between 98%-99.9%, generally intermittent use, pressure requirements are generally: 0.8Mpa below, and the flow requirements are not very large. Commonly used flow rates are: 50Nm3/h; 80 Nm3/h; 100 Nm3/h; 150 Nm3/h; 200 Nm3/h, the special nitrogen generator for the chemical industry produced by our company, with a purity of 99.5%-99.9%, is the most suitable for customers to use and meet customer requirements.
The chemical industry uses nitrogen as a raw material for chemical reactions: nitrogen is required to be of high purity, generally 99.99% purity.

Nitrogen output: 1~5000Nm3/hr
Nitrogen purity: 98%~99.999%
Nitrogen pressure: 0.6~0.9Mpa
Nitrogen dew point: -40°C~ -60°C
Technical features:
1. The raw material air is taken from nature, and nitrogen can be produced only by providing compressed air and power supply. The energy consumption of the equipment is low, and the operating cost is low.
2. The purity of nitrogen is easy to adjust, the purity of nitrogen is only affected by the amount of nitrogen exhaust, and the purity of ordinary nitrogen production can be adjusted arbitrarily between 95% and 99.99%; The high-purity nitrogen generator can be adjusted between 99% and 99.999%.
3. The equipment has a high degree of automation, fast gas production, and can be unattended. Start and shut down with just one button to press a button, and nitrogen can be generated within 10-15 minutes of turning on the machine.
4. The process flow of the equipment is simple, the structure of the equipment is compact, the area is small, and the equipment is adaptable.
5. The blizzard method is used to fill the molecular sieve to avoid the pulverization of the molecular sieve caused by the impact of high-pressure air flow, and to ensure that the molecular sieve can be used for a long time.
6. The digital flowmeter is a secondary instrument for industrial process monitoring with pressure compensation and high precision, and has the functions of instantaneous flow and cumulative calculation.
7. On-line detection of imported analyzer, high precision and maintenance-free.
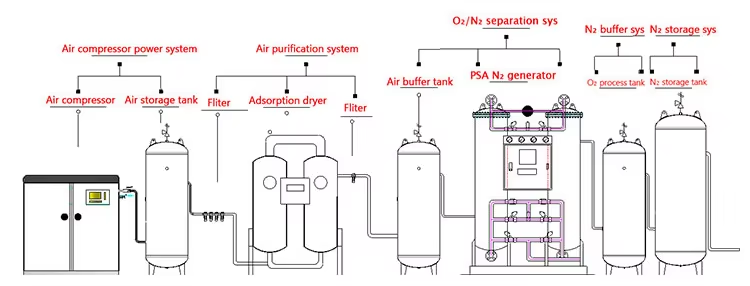
Application of nitrogen generator in chemical industry
It is mainly used for chemical material gas, pipeline purging, atmosphere replacement, protective atmosphere, product transportation, etc. It is mainly used in chemical industry, spandex, rubber, plastics, tires, polyurethane, biotechnology, intermediates and other work. Many chemical works do not require high nitrogen purity, and many purities greater than 98% can be used.
Acrylic oxidation explosion-proof, float glass process, protect the chemical industry in the chemical process to create an oxygen-free atmosphere to improve the safety of the production process, fluid transportation power source and other displacement, cleaning, sealing, leak detection, dry quenching of protective gas; Catalyst regeneration, petroleum fractionation, chemical fiber production and other gas oil industry to improve petroleum processing and essence process, oil storage and oil and gas field well pressurization, pipeline cleaning and purging, solvent recovery, etc.
Nitrogen purification of storage, containers, catalytic cracking towers, pipelines, etc.; air pressure leak test of pipeline system, etc.;
Offshore oil development; Inerting of gas covering, nitrogen injection, storage tanks, containers, etc.
The glass manufacturing industry prevents surface oxidation and furnace cooling in the glass manufacturing process.
Gas protection during float glass production process to prevent oxidation of tin bath. shielding gas in the production process of float glass;
Float glass work In the production process of float glass, the float medium is very easy to oxidize at the high temperature of the tin bath, the loss of tin is added, and various defects occur on the glass plate, so it is necessary to introduce the protective gas nitrogen into the tin bath, and participate in 5% ~ 10% of the hydrogen together, and the tin bath constitutes a recovery atmosphere, so that the tin oxide is restored to tin from scratch.